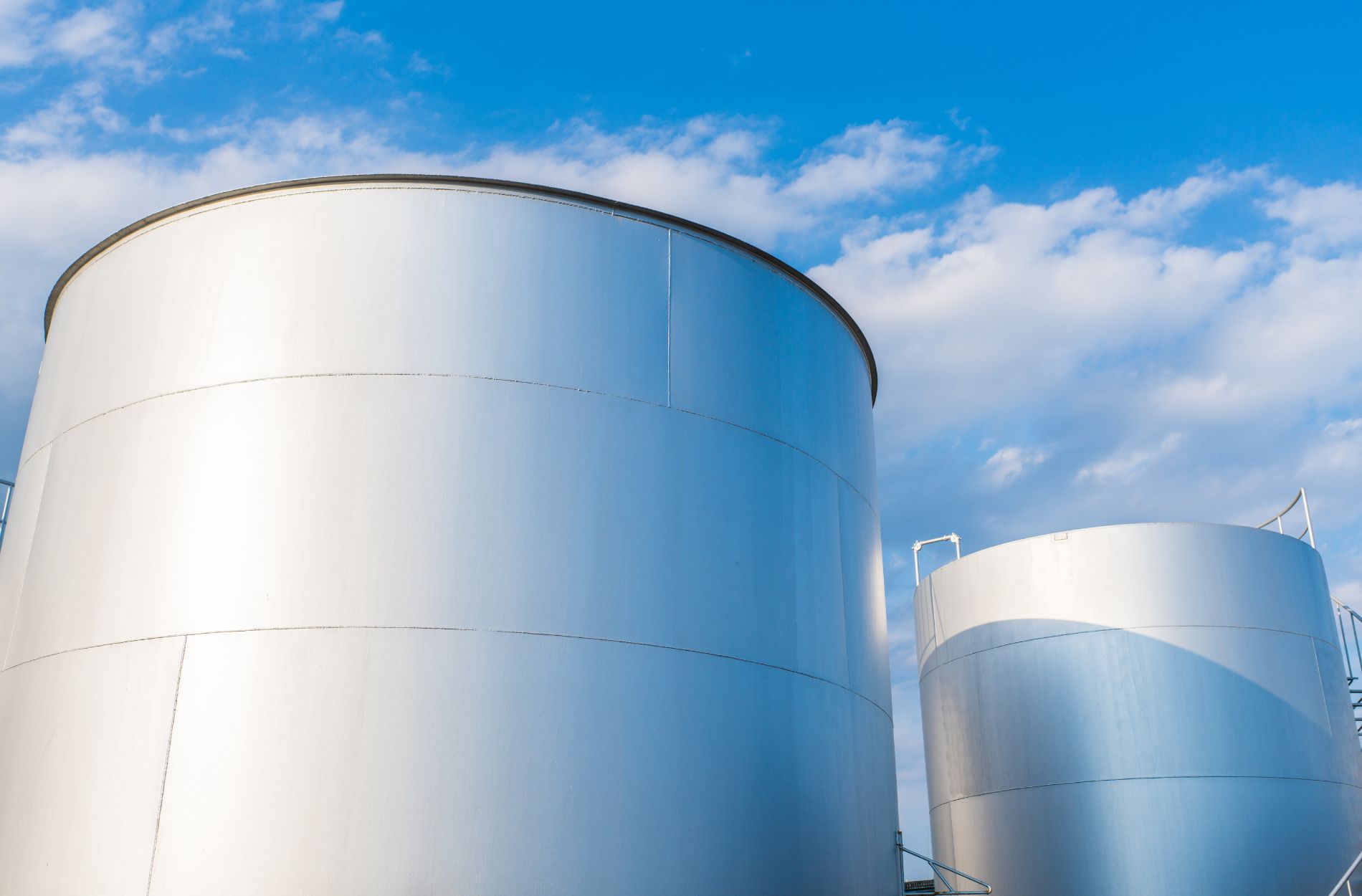
Building a strong and reliable tank begins with understanding the basics of tank construction. Tanks are crucial for storing substances safely, whether it’s water or industrial liquids. To make sure tanks stand the test of time and meet safety standards, it’s important to know what makes up their construction and how they function.
Materials and components play a big role in how tanks are constructed. Choosing the right ones ensures structural integrity and long-lasting performance. From steel frames to protective coatings, each element serves a purpose in keeping tanks safe and durable.
Adding tank liners is another important aspect of tank construction. Liners help protect the tank’s interior and maintain the quality of the stored contents. By using the right liner materials, tanks can be even more effective and secure. These basics provide a solid foundation for both new construction projects and maintaining existing tanks, ensuring they remain safe and efficient for their entire lifespan.
Key Components of Tank Construction
Tank construction involves several crucial components, each vital for ensuring that the tank remains strong and functional. The foundation of any tank typically starts with the frame, often made from robust steel. Steel frames provide exceptional strength and the flexibility needed to withstand various pressures and environmental conditions. Without a strong frame, tanks could fail under stress, leading to potentially disastrous consequences.
The next key component is the tank wall. Depending on the tank’s application, walls can be metal, concrete, or a composite material. These walls serve as the primary barrier between the tank’s contents and the outside environment. They must be constructed to resist corrosion and physical damage, preserving structural integrity over time.
Additionally, protective coatings are applied to the interior and exterior surfaces of tanks. Common coatings include epoxy and polyurethane, which safeguard the tank against chemical reactions and weather-induced wear. Coatings play an essential role in prevention, extending the lifespan of the tank and maintaining the quality of stored substances.
Finally, fittings and access points must be carefully designed and constructed to prevent leaks. Proper seals and gaskets ensure that all junctions remain secure, preventing valuable contents from escaping or contaminants from entering.
Types of Tank Liners and Their Uses
Tank liners are a crucial part of tank construction, providing an additional layer of protection to ensure contents remain safe and uncontaminated. Liners are often selected based on the type of material stored within the tank and the specific environmental conditions the tank might face.
Common liner materials include:
– Polyethylene Liners: These are widely used because of their versatility and affordability. They are ideal for storing water and many chemicals, offering a non-reactive surface that maintains purity.
– Rubber Liners: Known for their elasticity and resistance to abrasion, rubber liners are perfect for tanks that experience a lot of movement or need to store abrasive substances.
– PVC Liners: Cost-effective and easy to install, PVC liners are used for tanks that require protection against moisture and chemical exposure. They are commonly found in agricultural applications.
Using liners brings several benefits to tank construction. Liners protect the tank’s walls from corrosive materials, extending the overall life of the tank. They also help in maintaining the integrity of the stored substances by preventing cross-contamination and ensuring that the product quality remains high. Furthermore, liners can make tank cleaning much more efficient, as they provide a smooth surface that resists buildup and is easy to wash down.
Selecting the right liner is essential for optimising tank performance and ensuring the safety and integrity of both the tank and its contents.
Ensuring Durability Through Maintenance and Inspections
The longevity of a tank is heavily reliant on regular maintenance and thorough inspections. Keeping up with these practices ensures that tanks operate efficiently and safely throughout their lifespan. Regular maintenance involves tasks such as cleaning, repairing minor damages, and checking for signs of wear. Consistent cleaning of the tank’s interior prevents the build-up of residues that could compromise the tank material and the quality of stored products.
Inspections are equally crucial. They help in identifying potential issues before they escalate into costly repairs or serious safety hazards. Regularly checking the tank’s structural integrity involves looking for signs of corrosion and any abnormalities in the tank’s shape or functionality. Using techniques such as ROV inspections can provide detailed insights into areas that are difficult to reach, ensuring that every part of the tank is scrutinised.
Key inspection practices include:
– Visual Inspections: Regularly checking for visible signs of wear, rust, or damage.
– Ultrasonic Testing: Using sound waves to detect thickness changes and signs of corrosion.
– Leak Detection Tests: Ensuring no leaks are present which could lead to environmental damage or loss of contents.
A well-maintained tank not only lasts longer but also operates more safely, ensuring that stored materials are protected and that there are no unexpected operational disruptions.
Safety Considerations in Tank Construction
Safety is a paramount concern in tank construction. Designing tanks with safety features helps protect against both environmental and operational hazards, reducing risks for both personnel and stored materials. One of the primary safety features is the inclusion of pressure relief systems. These systems help manage internal pressure changes, preventing structural failures due to overpressure.
Proper grounding is essential for preventing lightning strikes, which could lead to catastrophic failures. Grounding ensures that electrical surges are safely directed away from the tank structure, reducing the risk of ignition in combustible environments.
Additional safety measures include:
– Spill Containment Systems: Designed to contain leaks or spills before they spread.
– Fire Suppression Systems: Equipped to control and extinguish potential fires quickly.
– Access and Egress Routes: Ensuring safe routes for maintenance staff and emergency exits.
By incorporating these safety features into tank design, operators can minimise risks and ensure a safer working environment. This proactive approach safeguards the integrity of stored substances while protecting the infrastructure and people involved.
Conclusion
Understanding tank construction basics is essential for anyone involved in the development, maintenance, or utilisation of tanks. By focusing on key components, the role of tank liners, regular maintenance, and advanced safety features, operators can ensure that their tanks remain reliable and efficient. Well-designed tanks incorporate robust materials and thoughtful construction practices to withstand various challenges and maintain their integrity over time.
For those looking to enhance the performance and safety of their tanks, ATM Tanks provides expert solutions. Our comprehensive services in tank construction and maintenance ensure your above-ground tanks meet all standards and perform optimally. Contact ATM Tanks today to explore our range of services and see how we can help protect and maintain your valuable assets.
- What to Do If Your Tank Leaks - May 25, 2025
- Effective Tank Inspection Techniques for Long-term Use - May 25, 2025
- Maximizing the Benefits of Tank Cleaning Services - May 25, 2025