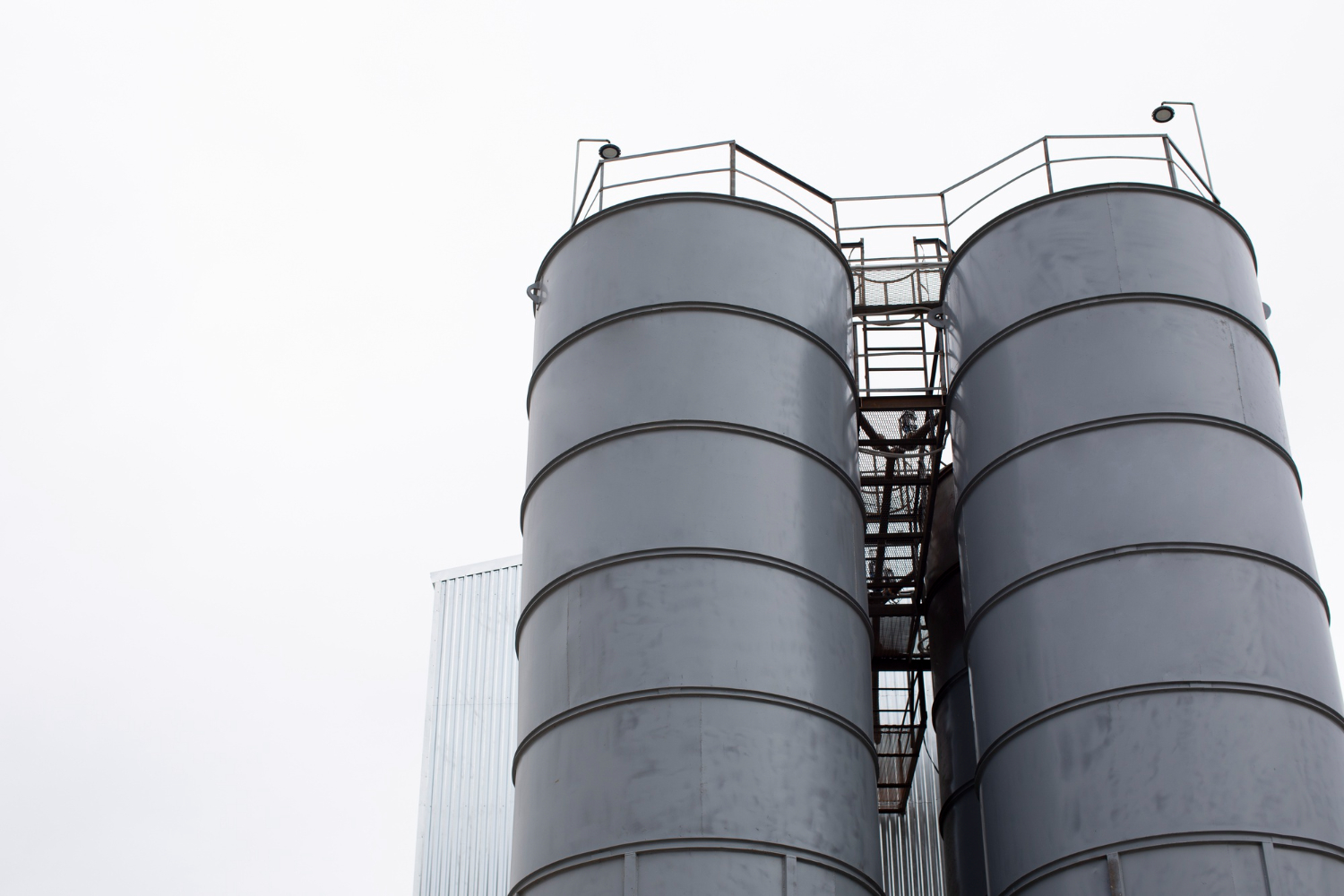
Constructing tanks that are both robust and long-lasting is pivotal in industries that rely on safe and secure storage. The secret to successful construction lies in the choice of materials and the methods employed during building. Each decision impacts the tank’s durability, efficiency, and overall lifespan.
Tanks must endure various environmental conditions and chemical exposures. Therefore, selecting the right construction materials is crucial. Steel, concrete, and advanced composites are among the popular choices, each offering distinct benefits and challenges. Aligning the choice of materials with the tank’s intended use ensures optimum performance.
Equally important are the construction techniques that lend strength and resilience to the tank structure. Innovations in technology offer new approaches to building and maintaining tanks. By incorporating the latest advancements and integrating maintenance considerations into the design, we can effectively extend the service life of any tank and reduce the risk of failures.
Key Materials for Tank Construction
When building a durable tank, choosing the right materials is crucial. Several materials offer longevity and resilience, helping to ensure tanks can withstand various conditions. Among the most common options are steel, concrete, and advanced composite materials.
Steel is a popular choice due to its strength and versatility. It can be formed into different shapes, making it suitable for various designs. However, steel is prone to corrosion if not properly treated, which can be a drawback in moist or chemical-heavy environments.
Concrete tanks offer excellent durability and are particularly effective in resisting fire and weather conditions. They are often used for water storage and can last for many years. The downside is their heavyweight and the need for regular maintenance to check for cracks that could lead to leaks.
Advanced composites, made from materials like fibre-reinforced polymers, are gaining popularity. They provide a balance of strength and lightweight properties, making them easy to install and maintain. They are resistant to corrosion, which is ideal for different storage needs. The higher initial cost might deter some, but the long-term benefits often outweigh this.
Choosing the right material depends on the tank’s specific needs and environment. Understanding the pros and cons of each option helps you make an informed decision tailored to your requirements.
Innovative Construction Methods
Modern construction methods are reshaping how tanks are built, making them more robust and reliable. These new approaches focus on enhancing strength while minimising environmental impact and reducing construction time.
Prefabrication is one such technique where tank components are produced in a controlled factory setting before being transported and assembled on-site. This method ensures consistency and quality, as each piece is crafted under ideal conditions. It speeds up the construction process and reduces the margin for error since each component is built to exact specifications.
Another forward-thinking method involves the use of slip forming, a continuous pouring process that constructs tank walls in a seamless manner. This technique ensures a uniform, sturdy structure, eliminating potential weak points caused by jointed segments.
Laser scanning and 3D modelling are technological advances that have vastly improved the precision of tank construction. They allow for detailed planning and visualisation before any physical work begins. By identifying potential issues early, these technologies minimise the risk of costly errors and enhance the overall structural integrity of the tank.
These innovative methods show how advancements in technology contribute to building tanks that meet modern demands for durability and efficiency. Incorporating such techniques ensures that tanks can handle current and future challenges efficiently.
Importance of Proper Lining and Coating
Lining and coating are critical components in tank construction, providing an extra layer of protection that enhances durability. The use of quality tank liners helps prevent leaks and ensures the stored contents remain uncontaminated. Different materials like rubber, polyethylene, or fibreglass are commonly used for liners, each offering varying degrees of flexibility and chemical resistance.
Proper liners not only keep the tank intact but also simplify maintenance. By acting as a barrier, they shield the tank’s structure from direct exposure to harsh substances, thus reducing wear and tear. This leads to fewer repairs and a longer lifespan for the tank.
Coatings and sealants are equally important, serving as a protective shield for tank interiors. They guard against corrosion, which is especially vital for metal tanks that are prone to rust. Advanced coatings can withstand extreme temperatures and chemical exposures, ensuring the tank remains secure under various conditions.
Choosing the right liner and coating depends on the tank’s purpose and the nature of the materials it will house. Implementing proper lining and coating techniques provides a defence against potential damages, maintains the integrity of the tank, and safeguards its contents.
Integrating Maintenance into Design
Designing tanks with maintenance in mind greatly improves their longevity and functionality. Tanks that are easy to inspect and repair are less likely to suffer from neglect-related issues, which can escalate into major problems over time. A well-thought-out design facilitates regular inspections and swift repairs, keeping the tank in good working order.
Considerations for accessible maintenance include placing inspection ports at strategic locations. These allow for easy access without the need for extensive disassembly. Ensuring that the design accommodates the latest inspection technologies, like ROV inspections, can also enhance maintenance efficiency.
Preventive measures integrated into design help in avoiding potential problems before they develop. Features such as built-in drainage systems, sloped floors for thorough cleaning, and corrosion-resistant materials work to minimise environmental impacts on the tank’s structure.
By incorporating these thoughtful design elements, tanks are better suited to endure the rigours of regular use while simplifying the maintenance process. This proactive approach keeps tanks performing optimally and extends their lifespan significantly.
Conclusion
Building durable tanks requires careful consideration of materials, methods, and maintenance strategies. Proper materials and innovative construction techniques lay a strong foundation while lining and coating protect against internal damage. Designing with maintenance in mind ensures that tanks remain functional and robust for years to come.
As you explore the best solutions for your tank needs, consider collaborating with experts who understand the intricacies of tank construction. ATM Tanks offers comprehensive services, from material selection to expert tank maintenance advice. Reach out to us today to learn how we can support your efforts in building and maintaining tanks that stand the test of time.
- The Importance of Industrial Tank Cleaning for Businesses - June 1, 2025
- Steps for Thorough Water Tank Cleaning - June 1, 2025
- Identifying and Repairing Common Tank Issues - June 1, 2025