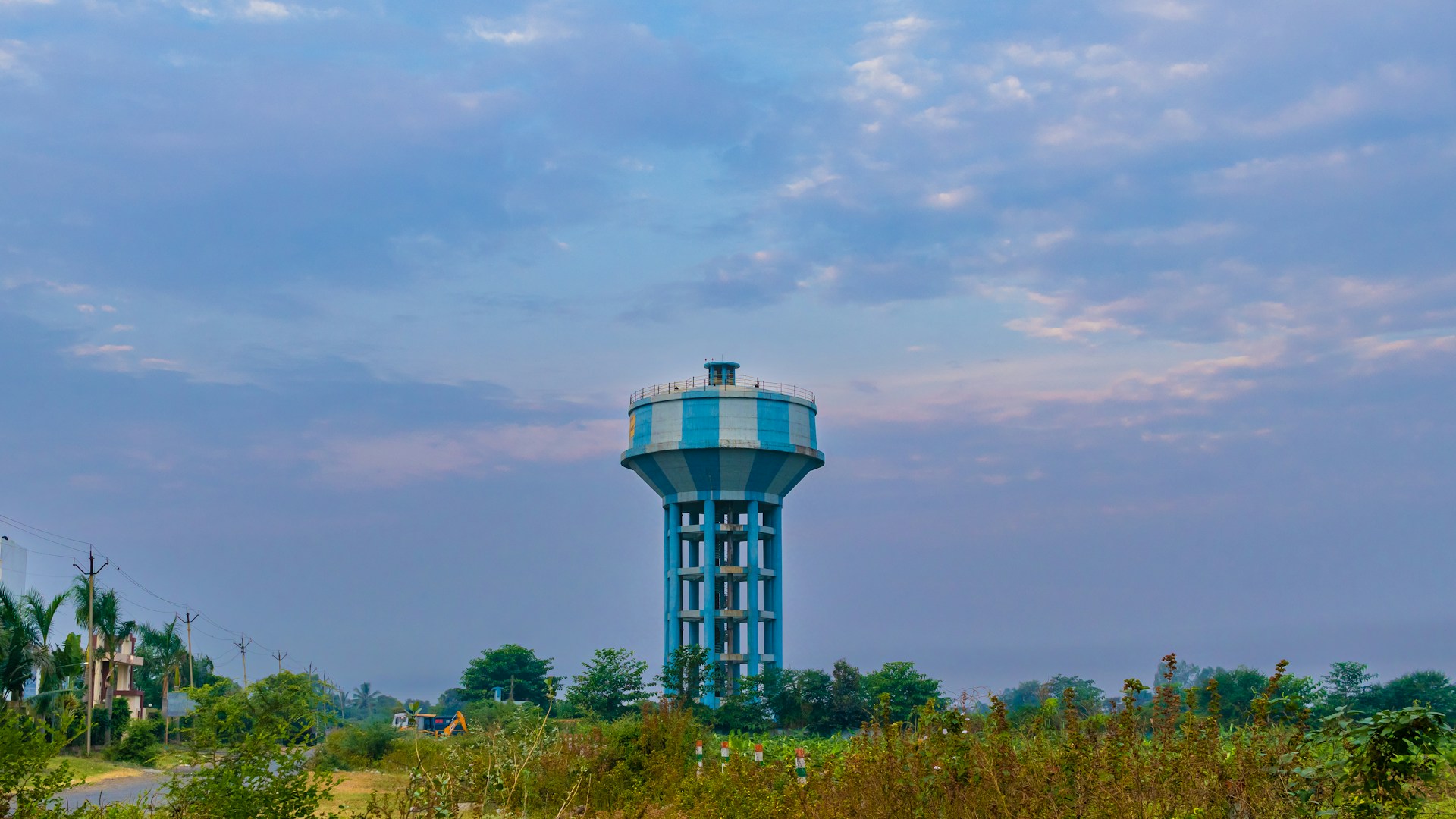
Tank liners play a vital role in safeguarding the interior of tanks against various forms of damage. They act as a barrier, protecting the tank from exposure to the substances stored inside, which can be particularly corrosive or reactive. Unfortunately, like any protective layer, tank liners can run into issues over time. Common problems include wear and tear, chemical reactions that degrade the material, and even separation of the liner from the tank walls. These issues, if left unchecked, might lead to more significant damage to the tank and potentially costly repairs.
Addressing tank liner problems in a timely manner is important for ensuring the longevity and effectiveness of tanks. Unattended damage can escalate into severe complications such as leaks or contamination of the substances within. To maintain the integrity of tanks, it is necessary to identify and resolve liner issues promptly. This involves understanding the common problems tank liners face and exploring innovative repair techniques that can fix these issues without major disruptions.
Common Tank Liner Issues
Understanding the typical problems associated with tank liners helps in preventing potential disasters. Below are some frequent issues tank owners encounter:
1. Cracking and Tearing: Over time, tank liners can develop cracks or tears due to constant stress and pressure or changes in the contents of the tank. These small imperfections can often escalate if not monitored and repaired promptly.
2. Chemical Degradation: Many substances stored within tanks might contain chemicals that gradually erode the liner material. This is a particularly sneaky problem as it might not be immediately visible but can cause significant long-term damage.
3. Delamination: This occurs when the liner starts to peel away from the tank’s internal walls. It can lead to pockets where fluids get trapped, resulting in potential corrosion and other damage.
Each of these issues requires proper attention from professionals who are trained to handle such problems effectively. Without professional intervention, these seemingly small issues can lead to bigger, more expensive fixes down the line.
Innovative Repair Techniques
Solving tank liner issues requires forward-thinking solutions. One modern method is seam welding advancements. This technique involves precisely welding the seams of damaged liners to ensure they are watertight. Advancements in welding technology have made this process quicker and more reliable, reducing downtime for tank owners.
Another approach is chemical bonding solutions. When liners suffer from minor tears or separations, specialised adhesives can effectively bond the material back together. These adhesives are formulated to resist the specific chemicals stored in the tanks, ensuring a long-lasting fix.
Finally, automated repair systems are gaining traction. These systems use robotics to perform repairs in tanks, especially in hard-to-reach areas. Automation increases efficiency and reduces human error, allowing tanks to get back to full operational capacity quicker than traditional methods.
Preventative Measures
Taking steps to prevent issues before they arise can save time and money. Regular inspection routines are a sound strategy. By routinely checking the condition of tank liners, potential problems can be spotted early. This proactive measure helps in maintaining the longevity of the liners.
Using high-quality liner materials is another effective preventative measure. Opting for materials that are resistant to chemical reactions and physical stress ensures the liners last longer and perform better.
Applying protective coatings on liners can also be a smart preventative strategy. These coatings act as an additional shield, absorbing any potential damage that comes from the tank’s contents, thus preserving the liner underneath.
Future Trends in Tank Liner Technology
The future of tank liner technology looks promising, with exciting developments on the horizon. One is the use of smart tank liners equipped with sensors. These sensors can detect changes in pressure or chemical composition, alerting owners to potential issues before they become serious.
Eco-friendly materials are also gaining popularity. As environmental concerns rise, there’s a push for liners made from sustainable and recyclable materials, helping reduce the environmental footprint of tank operations.
Durability is another focus, with enhanced durability through the incorporation of nanotechnology. These advancements could lead to liners that are not only tougher but also adaptive to different conditions, offering unparalleled protection.
Exploring these innovations and integrating them can make tank maintenance more efficient and eco-friendly. Implementing these new approaches could signal a major shift in how tanks are managed, offering both economic and environmental benefits.
For tank owners who want peace of mind knowing their tanks are well-protected, consider exploring the latest in tank liners. ATM Tanks can help ensure your systems are running smoothly and remain secure against damages. Whether it’s through smart liner technology or eco-friendly materials, reach out for solutions that keep your tank in top-notch condition.
- The Importance of Industrial Tank Cleaning for Businesses - June 1, 2025
- Steps for Thorough Water Tank Cleaning - June 1, 2025
- Identifying and Repairing Common Tank Issues - June 1, 2025